热塑性复合材料模压成型工艺:原理、优势与应用
热塑性复合材料作为一种先进的工程材料,在众多领域展现出卓越的性能优势。其模压工艺成型技术更是为高效、精准制造复杂形状部件提供了可靠途径。
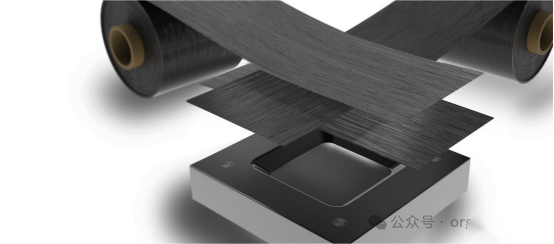
图1 热塑性连续纤维板材
原理
热塑性复合材料模压工艺,是将预浸有热塑性树脂的纤维增强材料层压板置于模具型腔中,通过加热、加压使其软化并在模具内压实,最终冷却固化成型的过程。模具通常由高强度金属制成,分为阴模和阳模,能够赋予产品精确的形状和尺寸精度。
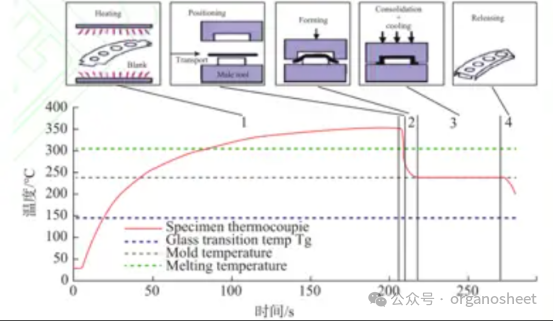
图2热塑性复合材料模压成型工艺流程
图2展示了热塑性复合材料模压工艺的基本流程,包括板材加热、板材入模、合模、冷却固化、脱模等步骤。
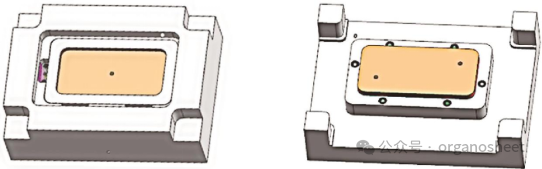
图3模具
图3为模具结构示意图,主要由阳模、阴模、顶杆等部分组成。阳模和阴模相互配合,形成模压制品的形状,顶杆则用于在脱模时将制品从模具中推出。
优势
热塑性复合材料模压工艺具有诸多优势。在成型效率方面,相较于热固性复合材料的固化过程,热塑性材料加热熔融后快速冷却成型,大大缩短了生产周期,适合大规模批量生产,能有效降低制造成本。
材料性能上,热塑性复合材料具有更好的韧性和抗冲击性能,其可回收性也符合现代环保理念,减少了材料浪费和对环境的负担。而且,该工艺能够制造出形状复杂、尺寸精度高的部件,产品表面质量优良,减少了后续加工工序,进一步提高了生产效率和经济效益。
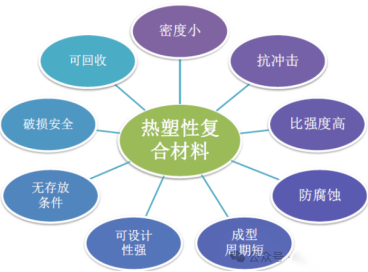
图4热塑性复合材料优势
应用
在汽车工业中,热塑性复合材料模压成型的零部件广泛应用于车身结构件、内饰件等。例如汽车悬挂系统部件,由于其良好的抗疲劳性能,能在负载的路况和频繁的应力作用下保持稳定的性能,从而提升底盘系统的可靠性和耐久性。
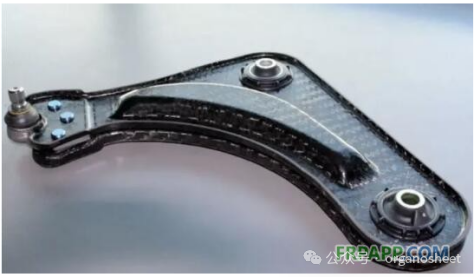
图5悬架控制臂
航空航天领域,对材料的性能和重量要求极高。热塑性复合材料模压成型的机翼前缘、机身舱门等部件,在保证结构强度的同时,显著降低了飞机的自重,为航空航天事业的发展提供了有力支持。
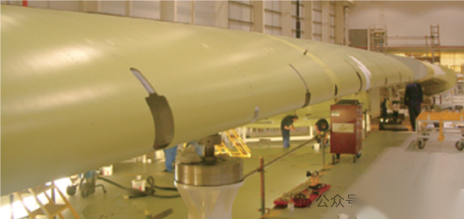
图6机翼前缘
电子电器行业,利用该工艺生产的精密外壳和散热部件,凭借其良好的尺寸稳定性和绝缘性能,满足了电子产品日益小型化、高性能化的需求,同时提高了产品的耐用性和可靠性。
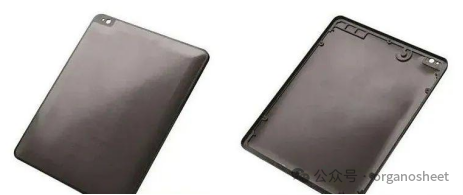
图7笔记本外壳
展望
尽管热塑性复合材料模压工艺前景广阔,但也面临一些挑战。例如,原材料成本相对较高,需要进一步优化生产工艺和扩大生产规模来降低成本;对模具设计和制造要求较高,需要高精度、高性能的模具来保证产品质量;工艺参数的精确控制也需要先进的设备和技术支持,以确保产品性能的稳定性和一致性。
热塑性复合材料模压工艺成型凭借其独特的优势,在多个领域发挥着重要作用,随着技术的不断创新与突破,有望在未来制造业中占据更加重要的地位,为推动各行业的发展贡献更大的力量。